About two years ago, I started running into a problem with our print farm: the filament sensors on the printers began to fail.
It was a very specific failure: the filament sensors started producing erroneous out-of-filament reports. That means that the printer would pause and beep, requesting new filament since it had run out. But that wasn’t the case: there was still plenty of filament available for the printer.
In other words, the printer filament sensors were producing false positives.
One by one, the printers started producing this error. After a year, half of the printers on the farm didn’t have a functional filament sensor, since they all produced false positives.
If you have diagnostic training (engineer, doctor, mechanic, business analyst, etc.), this will probably strike you as interesting. The same failure on a large number of identical machines points to some kind of systemic issue. The question is: what is it?
After two years, I finally have the answer.
My first instinct was, of course, to see if anybody else had the same issue. I quickly discovered a sad truth: if you Google the problem, nobody appears to know the cause. There is a lot of conjecture, but nobody actually knows.
I next investigated possible electrical causes. The wire harness seemed like a prime location for wire abrasion. The connectors also jostled a lot, so perhaps they were loose. It could have also been some kind of board soldering failure.
On every single printer that experienced this problem, that wasn’t the case. The electronics were in good working order.
I finally had a breakthrough, randomly, as breakthroughs often occur. Yet another printer of mine started suffering from the same false positive issue, and coincidentally, at exactly the same time, the filament jammed and broke inside the adapter-printer.
I removed the adapter-printer on the most-recently-misbehaving printer, and took a look at it. And that’s when I noticed something.
I grabbed all of the other printers with the same false positive issue, and removed their adapter-printers, too. Here are three of them:
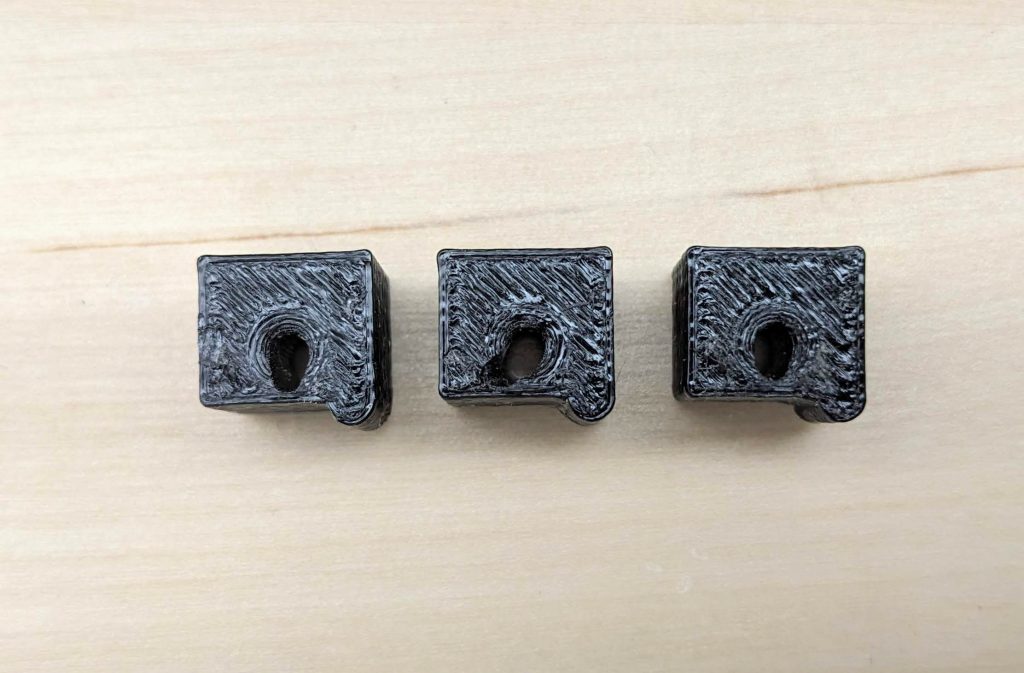
The hole for the filament, which is supposed to be round, has become significantly abraded.
I’d cracked it.
So, what does this mean? Why is this abrasion important?
The way that the adapter-printer works is that filament runs through that hole, and there’s a small ball tensioned against the filament. If the filament runs out, the ball moves into the space that was once occupied by the filament, which trips a sensor.
However, all of the printers with false positives had abrasion wear on their adapter-printers, and, crucially, the abrasion was farther away from the ball.
That means that, sometimes, the filament would slip into that abraded channel, and the ball would move slightly into the space occupied by the filament. It would sometimes be enough to trip the filament sensor.
So, with hypothesis in hand, I replaced all of the adapter-printers. I’m happy to report that every single printer is now functioning again, with no false positives after many hours of printing.
So, what’s the lesson here?
I rely on the experiences of others a lot to help me. When I write code, I use StackOverflow. When I make circuits, I rely on appnotes and open-source schematics.
Then, there’s a certain point at which you step into the uncharted. No guidance, no map, nothing.
I had a bit of luck to help me, there’s no doubt. It was lucky that I looked at that part. However, when I looked at it, I also formulated a testable hypothesis.
It’s that diagnostic, scientific mindset that enables people to discover and fix things, especially when there’s very little assistance forthcoming.
That’s my big takeaway.
And also: if your Prusa printer’s filament sensor is producing false positives, check for wear on the adapter-printer, and replace it if necessary.